ADVANCED CERAMICS TECHNOLOGIES

TECHNICAL CERAMICS MANUFACTURER
Technische Keramikherstellung: Eine Vielzahl von Herstellungsverfahren wird bei der Produktion von technischer Keramik eingesetzt, um den Anforderungen des Endprodukts und der Anwendung gerecht zu werden. Hier sind einige der gängigsten Verfahren im Überblick:
Diese Verfahren sind nur einige Beispiele für die Herstellung von technischer Keramik. Die Auswahl des geeigneten Verfahrens hängt von verschiedenen Faktoren ab, wie der Art des Endprodukts, der erforderlichen Stückzahl und den spezifischen Anforderungen der Anwendung.
Pressen von technischer Keramik
Pressen ist das vorherrschende Verfahren zur Herstellung von technischer Keramik. Es beinhaltet das Verdichten von pulverisiertem Rohmaterial unter Verwendung von Druck und Hitze. Anschliessend kann die Keramik weiterbearbeitet werden, beispielsweise durch Sintern, Pressen oder Schneiden.
CIM Keramikspritzguss
Spritzgiessen ermöglicht die Herstellung komplexer Keramikteile. Dabei wird Keramikpulver unter hohem Druck und Hitze in eine Form eingespritzt. Das resultierende Teil erfordert in der Regel eine zusätzliche Sinterung und Weiterverarbeitung.
Keramik Extrusion
Die Extrusion wird oft eingesetzt, um Rohre, Stangen und andere längliche Keramikteile herzustellen. Hierbei wird die Keramik durch eine Düse gepresst, um die gewünschte Form zu erzeugen.
Sprühtrocknung
Die Sprühtrocknung wird zur Herstellung dicker Schichten oder Beschichtungen verwendet. Dabei wird flüssiges Keramikmaterial zerstäubt und anschliessend getrocknet sowie verdichtet.
Sol-Gel Verfahren
Das Sol-Gel-Verfahren ermöglicht die Herstellung dichter und glatter Keramikoberflächen durch kontrollierte chemische Reaktionen.
Heisspressen
Beim Heisspressen werden komplexe Keramikteile aus bereits gesintertem Rohmaterial hergestellt. Das Keramikmaterial wird unter hohem Druck und Temperatur geformt.
PROCESS STEPS THE TECHNICAL CERAMICS

Raw materials and powder
Basic requirements of production and the most economical manufacturing process determine the selection of raw materials (type, purity, grain size and specific surface) as well as other auxiliary materials.
Alumina
Zirconium oxide
Silicon nitride
Silicon carbide

Shaping
Here, the powder particles are compressed and brought into a coherent shape that has sufficient strength for subsequent handling.
The selection of the suitable shaping process is usually based on economic considerations (rational production).
Dry pressing
Extrude
Foil casting
Injection molding
Micro injection molding
Isostatic pressing
3D printing LCM
Alumina
Zirconium oxide
Silicon nitride
Silicon carbide

Quality inspection
Consistent quality is based on qualified manufacturing processes, the regulations and results of which are routinely monitored and recorded.
Optically
Dimensional check
Crack testing
Strength test
Roughness testing
Screwing test
Surface inspection
Hardness test
...

Mass preparation
The ceramic manufacturer obtains the raw materials and carries out all further processing steps himself or the ceramic manufacturer purchases processable materials and begins the ceramic process with the shaping.
Grind
Mix
Filter
Granulate
Plasticizing
Spray drying

Green processing White processing
Green processing takes place on dried components that still contain organic additives.
The white processing takes place on pre-fired components that are free of organic additives. The strength is determined by the pre-firing.
Milling
Rotate
Drill
Saws
grind
Lapping
polishing
Honing
Metallizing
Glazing
Assembly
substitution
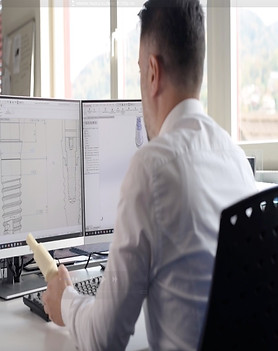
Engineering
In solving a technical problem, the engineer or designer must design technical elements. In the case of ceramic materials, he must pay particular attention to the required material-specific design.
Determine requirements
construction
Technical drawing
application
Determine quality
Determine the manufacturing process
Determine prices
Define quantities
Determine material (Al2O3, ZrO2, SiC, Si3N4)
Send offer

Finishing
Hard machining
The final processing or hard processing takes place on completely fired components, which have already been brought as close as possible to the final dimensions through the shaping, green or white processing. The tightest tolerances can be achieved by removing finishing processes.
grind
Lapping
polishing
Honing
Metallizing
Glazing
Assembly
substitution
...