ADVANCED CERAMICS TECHNOLOGIES

CERAMIC MATERIALS - TECHNICAL CERAMICS
TECHNICAL CERAMIC MATERIALS
Engineering ceramics can be made from a variety of materials depending on the desired properties and applications. Some of the most common materials are:
-
Alumina (Al2O3): This is the most commonly used material for technical ceramics. It has high strength, hardness, rigidity and chemical resistance. It is often used for applications in the electronics, mechanical and chemical industries.
-
Silicon Carbide (SiC): This material has high strength, hardness and resistance to high temperatures and chemicals. It is often used for applications in the automotive, aerospace and energy industries.
-
Silicon nitride ceramic (Si3N4) is a material from the group of technical ceramics. It is characterized by high strength, hardness, fracture toughness and temperature resistance. In addition, Si3N4 has good corrosion resistance, electrical insulation properties and low density.
-
Aluminum nitride (AlN): This material has high thermal conductivity, electrical insulation ability and resistance to high temperatures. It is often used for applications in the electronics and automotive industries.
-
Titanium oxide (TiO2): This material has a high level of transparency, high resistance to chemicals and weathering, as well as high hardness and scratch resistance. It is often used for applications in the optical industry and coating technology.
-
MACOR is a special type of glass ceramic, also known as machinable glass ceramic. It is a material characterized by its excellent machinability and high chemical resistance.
There are many other materials that can be used to manufacture technical ceramics. The choice of material depends on the specific requirements of the application, including the required mechanical, thermal, electrical and chemical properties.

Aluminum oxide is the most commonly used ceramic material. Thanks to its very good electrical insulation, dielectric strength and high temperature resistance up to 1750°C, it is ideal for electrical applications and high-temperature applications.
THE ADVANTAGES OF ALUMINUM OXIDE CERAMIC
-
High strength
-
High hardness
-
Good temperature resistance
-
High wear resistance
-
High corrosion resistance up to high temperature ranges
-
High biocompatibility
-
Excellent tribological properties
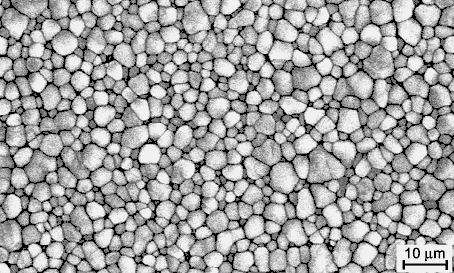
Zirconium oxide is the high-performance material among the oxide ceramics. It features exceptional fracture toughness, high wear and corrosion resistance, and low thermal conductivity.
THE ADVANTAGES OF ZIRCONIA CERAMIC
-
Very high fracture toughness
-
Very high bending and tensile strength
-
High wear resistance
-
High compressive strength
-
Very low thermal conductivity
-
Thermal expansion similar to cast iron
-
Modulus of elasticity comparable to steel
-
oxygen ion conductivity
-
Very good tribological properties
-
Excellent surface finish and sharp edges possible

The optimal properties of both materials are realized in our mixed oxide ceramics .
-Main component ZrO2 is called ATZ (Alumina Toughened Zirconia)
-Main component Al2O3 hot ZTA (Zirconia Toughened Alumina)
THE ADVANTAGES OF MIXED OXIDE CERAMICS
The background of the mixtures is to combine the "good" properties of both oxides:
The great strength and toughness of zirconia with the hardness and wear resistance of alumina.
With a suitable proportion of ZrO2 in the ZTA material, the high electrical insulation of the Al2O3 is retained.

Light and yet extremely stable – that is what characterizes silicon carbide. Also known as silicon carbide or silicon carbide, the ceramic material shows excellent properties for a wide variety of applications. Silicon carbide components are ideal for applications in which wear resistance, high rigidity, corrosion resistance and temperature resistance are of essential importance.
THE BENEFITS OF SILICON CARBIDE
-
Outstanding chemical resistance
-
High strength
-
Excellent corrosion resistance even at very high application temperatures
-
Excellent high temperature mechanical properties
-
Good thermal shock resistance
-
Low thermal expansion
-
Very high thermal conductivity
-
High wear resistance
-
Very high rigidity

The ceramic material silicon nitride (also: silicon nitride) is the all-round talent among technical ceramics. With its high strength and fracture toughness, very good thermal shock resistance and its excellent wear and impact resistance, silicon nitride is suitable for a wide variety of applications.
THE ADVANTAGES OF SILICON NITRIDE CERAMIC
-
Very good strength up to high temperature ranges (>1200°C)
-
Excellent wear and impact resistance
-
High hardness
-
fracture toughness
-
Low thermal expansion
-
Relatively low thermal conductivity
-
Very good thermal shock resistance
-
Very good chemical resistance
-
Electrically conductive material available
_edited.jpg)
It combines the performance of a technical ceramic with the versatility of a high-performance plastic - making it an excellent machinable material. Even the most demanding fittings and the smallest precision parts can be manufactured by turning and milling. When the performance of a technical ceramic is required and the application requires the manufacture of a requires a complicated shape, Macor® glass ceramic is the ideal material. It helps to significantly reduce the time between development and deployment, thereby reducing the cost.
THE ADVANTAGES OF MACOR® / GLASS-CERAMIC
-
Cost effective to process
-
Most complex shapes possible
-
Radiation Resistant
-
Low thermal conductivity
-
Very high service temperature
-
Good electrical insulator
-
No porosity and no outgassing
-
Short throughput times
-
No glaze firing required